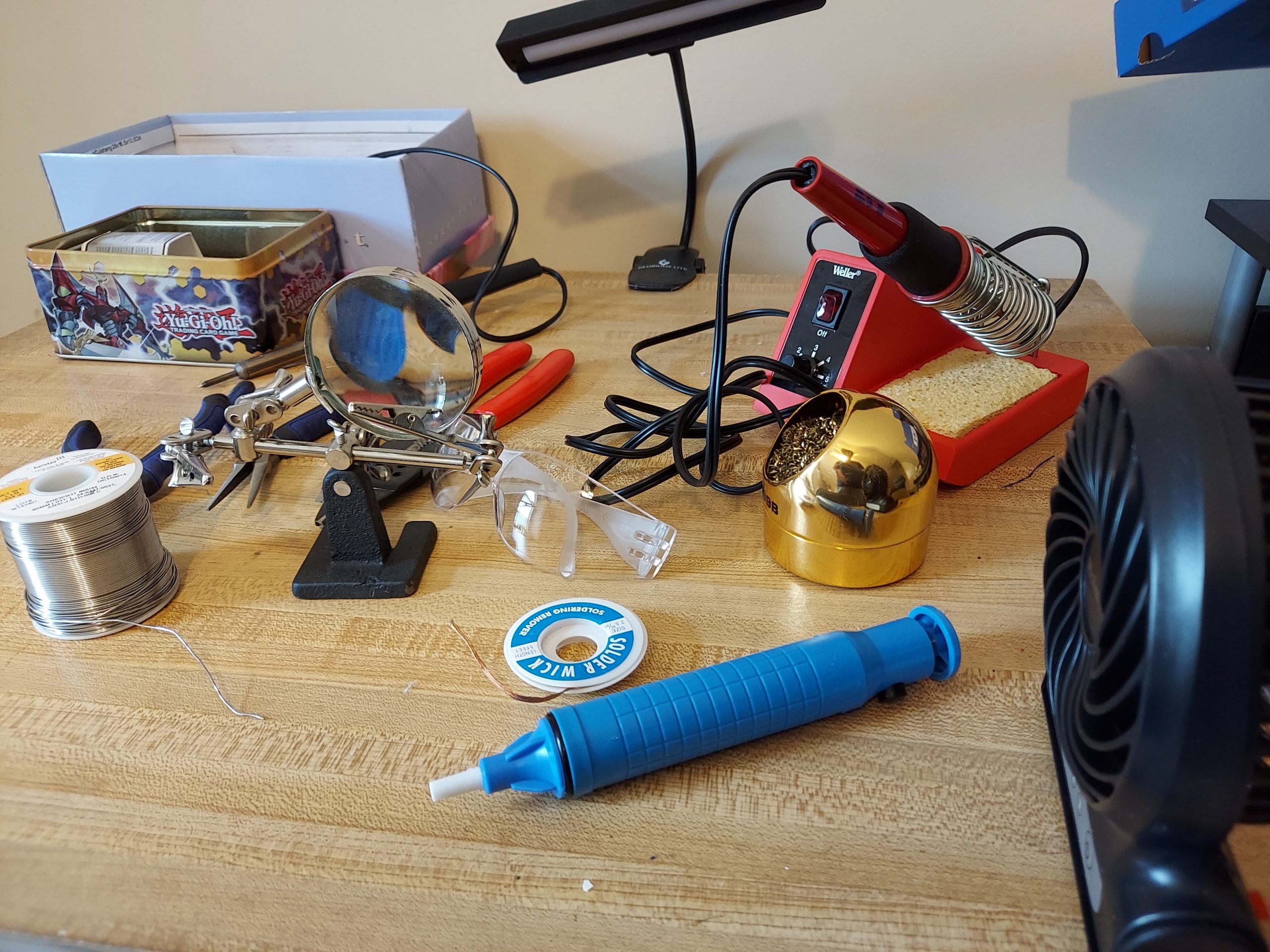
A Walk Through of My Soldering Station
When working on electronics it is important to keep a tidy, and safe workspace. I thought I would show what my bench looks like as an example for others who are just starting out on their tinkering journey.
Desk & Chair
I recommend a desk that is at a comfortable working height, that is clean and resistant to static & fire/heat. An adjustable padded chair, such as an office chair, that can keep your knees at 90 degrees and help maintain good posture is key for avoiding long-term injuries.
Soldering Iron
I have both a cheap RadioShack soldering iron and a decent Weller adjustable temperature iron (WLC100 Soldering Station). It is okay to start with the cheap one until you can upgrade. The basic requirements are an iron that is at least 25 watts. Most come with a conical tip (useful for small joints), but wedge tips are better for maintaining heat, which is better for good soldering joints.
Solder & Flux
Even though Leaded solder is toxic and not used in commercial products, it is still the go-to for electronics hobbyists in the United States due to its low melting point and ease of creating good soldering joints. Lead-free is available and recommended from a safety standpoint. Solder with 60% tin (often called 60/40) is seen as the best solder, due to its lower melting point. Flux-core solder, as the name suggests, contains flux, often rosin/resin, which aids in creating good solder joints.
Helping Hands
Circuits and components get hot when soldering, so helping hands are a must. There are several styles depending on your needs and budget. I recommend one with alligator clips and a magnifying glass as a bare minimum. Upgrades include a mirror with a light, a fan attachment, and different style clips. There is even a silicone connector holder called a Hot Holder that is a must-purchase for anyone creating a variety of custom cables.
Fan & Airflow
A fan is a necessity in order to avoid inhaling fumes from the heated solder. Airflow must be directed away from the working area, which means there must be at least one open window/door in addition to the fan if you are working indoors.
Light
I recommend an adjustable desk lamp for any soldering project. I inevitably find myself in rooms with insufficient light and a desk lamp is key for inspecting tiny soldering joints.
Wirecutters & Strippers
Generic wire cutters are so important, that one might even have multiples, like angled wire cutters for circuits in a small housing. While some use pocket knives for wire strippers (to trim the plastic coating off wires), I prefer having a multi-gauge wire stripper.
Sponges, solder suckers, scrapers, wicks
Over the course of soldering, the solder coating the tip of the soldering pen will discolor and become ineffective. To clean the old solder one can use a small wet sponge, it often comes with the soldering kit, or a brass wool solder scraper. I use both. Solder suckers and solder wicks are useful when one accidentally uses too much solder on a joint and bridges two wires together. Solder wicks are copper braids that soak the excess solder, while solder suckers are retractable pen that sucks a small chunk of solder.
Other Helpful Tools
With tiny components, fingers are often too clumsy or too large, that is why I have tweezers and needle nose pliers in my kit. I also keep cotton swabs and isopropyl alcohol to clean up my finished board. Multimeters are useful to double-check connections within the circuit. If there are any accidental shorts or missed joints, the multimeter should find them.
Safety notes
Wear safety glasses to protect your eyes from flying wire fragments and hot solder. Use a bubble wand to find out if the airflow of your work area is directed away from your face. If the bubbles are floating towards the open window, you are all set. When the bubbles just hang in the air, it is time to add another fan or open another window/door. Take regular breaks from the soldering and take a short walk. It is not good for your overall health to work in a fume-filled and cramped position (even when trying to maintain good posture). If you have a drink in your work area, make sure that it is covered (to prevent contamination), and wash your hands before handling any food or drink after soldering. Overall it is good practice to wash your hands after soldering.